Digital Pressure Gauge WIKA
A digital pressure gauge displays the acting pressure in an integrated digital display. WIKA offers digital pressure gauges for general industrial applications and also for use in the field of testing and calibration. The indicator cases of our digital pressure gauges are rotatable for easy viewing if required and thus always ensure good readability. In addition, and intrinsically safe versions and instruments with wireless interface versions are also available.
Digital pressure gauge Model CPG1500
The model CPG1500 precision digital pressure gauge takes the concept of an analog gauge and raises it to a level only matched by digital calibrators. The accuracy of digital measurement technology and the simplicity of an analog gauge are combined together to create the digital pressure gauge CPG1500, which in terms of performance, ease-of-use, and instrument features, is unmatched in the pressure measurement market.
Accuracy
The digital pressure gauge CPG1500 offers an accuracy of 0.1 % of span (optional 0.05% up to 0.025% of span) and is temperature-compensated in the range of -10 … +50 °C (14 … 122 °F). Readings can be displayed in one of 21 standard units or also in customer-specific units, so that intricate conversion is avoided.
Sampling rate
The measuring rate can be user-defined to match the type of measurement required. Standard applications usually use three measured values per second. If required, this rate can also be set to 50 measured values per second. Via an energy-saving function, the digital pressure gauge CPG1500 switches automatically into “sleep” mode, in this mode, the battery life can be increased up to 2,500 hours.
Features
Through the new and innovative menu navigation, simple operation is ensured. The clear display, with integral bar graph display and large text area, assists with the effective analysis of the widest variety of measuring points. With the MIN/MAX function, the highest and lowest pressures can be accessed immediately and saved automatically.
Applications of the digital pressure gauge
- Oil and gas industry
- Maintenance and service facilities
- Calibration service companies and service industry
- Simple calibrations directly on site
Special features of the digital pressure gauge
- Measuring ranges up to 0 … 1,000 bar (0 … 150,000 psi) (vacuum and absolute pressure ranges also available)
- Accuracy: Up to 0.025 % (incl. calibration certificate)
- Intrinsically safe version
- Logger function with up to 50 measured values per second
- Communication with WIKA-CAL software over WIKA-Wireless
Measuring range
Type of pressure
- Gauge pressure, absolute pressure (up to 20 bar abs. (290 psi abs.)) and vacuum measuring ranges
Gauge pressure (bar)
0 … 0.1 / 0 … 0.25 / 0 … 0.4 / 0 … 0.6 / 0 … 1 / 0 … 1.6 / 0 … 2.5 / 0 … 4 / 0 … 6 / 0 … 10 / 0 … 16 / 0 … 25 / 0 … 40 / 0 … 60 / 0 … 100 / 0 … 160 / 0 … 200 / 0 … 250 / 0 … 400 / 0 … 600 / 0 … 700 / 0 … 1,000 / 0 … 1,600 / 0 … 2,500 / 0 … 4,000 / 0 … 6,000 / 0 … 7,000 / 0 … 8,000 / 0 … 10,000
Absolute pressure (bar)
0 … 0.25 / 0 … 0.4 / 0 … 0.6 / 0 … 1 / 0 … 1.6 / 0 … 2.5 / 0 … 4 / 0 … 6 / 0 … 7 / 0 … 10 / 0 … 16 / 0 … 20 / 0 … 25 / 0 … 40
Vacuum and +/- measuring ranges (bar)
-0.25 … +0.25 / -0.4 … +0.4 / -0.6 … +0.6 / -1 … 0 / -1 … +0.6 / -1 … 1.5 / -1 … 2.5 / -1 … 3 / -1 … 5 / -1 … 7 / -1 … 9 /-1 … 10 / -1 … 15 / -1 … 24 / -1 … 25 / -1 … 39 / -1 … 40
Sensor technology
Compensated temperature range
- -10 … +50 °C (14 … 122 °F)
Process connection
- G ½ B, G ¼ B, ½ NPT, ¼ NPT, G 1 B flush, G ½ B flush
- M16 x 1.5 female with sealing cone
- M20 x 1.5 female with sealing cone
- 9/16 – 18 UNF female F 250-C
Pressure medium
- All liquids and gases which are compatible with 316 stainless steel
Adjustment
- Offset and span factor adjustable
Display
- 5 ½ digit 7-segment display including a large matrix area for an auxiliary information Bar graph, 0 … 100 % Selectable backlighting
Rotatable case
- The case is rotatable by 330°.
Resolution
- 4 … 5 ½ digit; adjustable; dependent on the selected pressure unit
Material
Wetted parts
- ≤ 1,000 bar: Stainless steel 316
- > 1,000 bar: Stainless steel 1.4534
- -1 … < 40 bar: Stainless steel 316
- > 40 … 1,000 bar: Stainless steel 316 + Elgiloy cells 2.4711
Case
- Aluminum die-casting, nickel-plated
Voltage supply
- 3 x 1.5 V AA alkaline batteries
Maximum voltage
- DC 4.95 V (spark ignition)
Battery life
- typical 2,000 … 2,500 h (without backlighting and WIKA-Wireless not active)
Frequency range
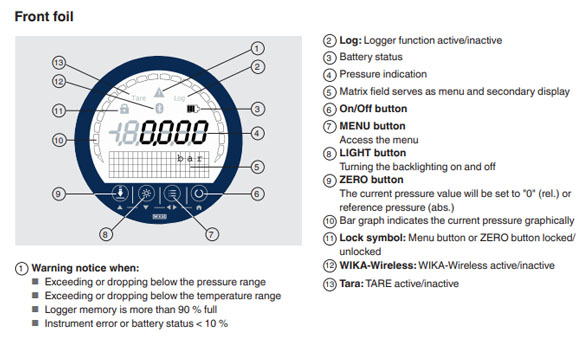