Positive Displacement Compressor
An air compressor is a device which sucks the atmospheric air and pressurizes it and to a higher pressure and gives it to the system. Compressors can be classified as
- Positive displacement
- Dynamic displacement
difference between positive displacement compressors and dynamic compressors
A positive displacement compressor, compress the air by forcing air into a compression chamber and by decreasing its volume
A dynamic displacement compressor compresses the air by imparting the kinetic energy of the rotating parts to the air. Centrifugal and axial compressors are dynamic compressors.
The basic one-line difference between positive displacement compressor (PDC) and dynamic compressor (DC) lies in the fact of how they apply the pressure on a fluid. In PDC a mechanical linkage reduces the volume of fluid physically to increase the pressure whereas in DC the fluid is provided some velocity which undergoes a diffuser resulting in the increase in pressure.
An easy way to memorize the fact is in the name itself. Positive displacement compressor means a system which compresses the air by the displacement of a mechanical linkage reducing the volume (since the reduction in volume due to a piston in thermodynamics is considered as a positive displacement of the piston). The dynamic compressor brings out a change in the velocity of the fluid eventually resulting as the rise in pressure.
Types of positive displacement compressor
Piston Compressors
The piston compressor is the oldest and most common type of industrial compressor. It’s available in single-acting or double-acting, oil-lubricated or oil-free variants, with various numbers of cylinders in different configurations.
Oil-free piston compressors have piston rings made of polytetrafluoroethylene (PTFE) or carbon. Alternatively, the piston and cylinder wall can be profiled as on labyrinth compressors. Larger machines are equipped with a crosshead and seals on the gudgeon pins, and a ventilated intermediate piece to prevent oil from being transferred from the crankcase into the compression chamber. Smaller compressors often have a crankcase with bearings that are permanently sealed.
Rotary Screw Compressors
Developed in the 1930s, rotating displacement compressors in twin screw form have two main parts — the male and female rotors, which rotate in opposite directions while the volume between them and the housing decreases. Each screw element has a fixed, built-in pressure ratio that is dependent on its length, the pitch of the screw and the form of the discharge port. To attain maximum efficiency, the built-in pressure ratio must be adapted to the required working pressure.
Modern oil-free screw compressors have asymmetric screw profiles that reduce internal leakage and improve energy efficiency. Their external gears are most often used to synchronize the position of the counter-rotating rotors. Because the rotors never come in contact with one another, no lubrication is required in the compression chamber and the compressed air produced is completely oil-free.
Liquid-injected screw compressors use liquid lubrication in their compression chamber and often with their compressor bearings as well. The liquid cools and lubricates the compressor element’s moving parts, which cools the air being compressed and reduces the return leakage to the inlet. Today, oil is the most commonly used liquid due to its good lubricating and sealing properties. Other liquids used include water.
Tooth Compressors
Tooth compressors contain two rotors that rotate in opposite directions inside a compression chamber. Its compression process consists of intake, compression and outlet phases. During the intake phase, air is drawn into the compression chamber until the rotors block the inlet.
The air is then compressed in the compression chamber, which gets smaller as the rotors rotate during the compression phase. In its final phase, the outlet port is blocked during compression by one of the rotors while the inlet is open to draw in new air into the opposite section of the compression chamber.
Scroll Compressors
A scroll compressor is usually a type of oil-free orbiting displacement compressor, which compresses a specific amount of air into a continuously decreasing volume. The compressor element consists of a stator spiral fixed in a housing and motor-driven eccentric, orbiting spiral.
The spirals are mounted with 180° phase displacement to form air pockets with a gradually varying volume, which provides the scroll elements with radial stability. When the orbiting spiral moves, air is drawn in and captured in one of the air pockets, where it is gradually compressed as it moves toward the center.
Vane Compressors 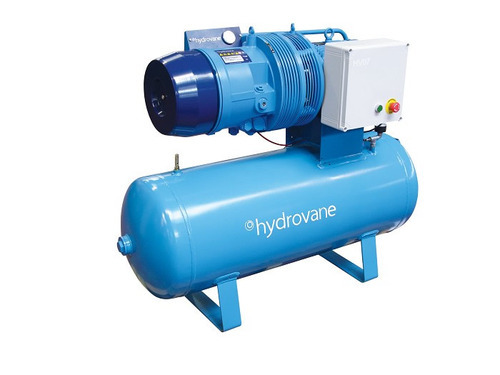
Most vane compressors are oil-lubricated and operate using the same principle as many compressed air expansion motors. A rotor with radial, movable blade-shaped vanes is eccentrically mounted in a stator housing.
When it rotates, the vanes are pressed against the stator walls by centrifugal force. Air is drawn in while the distance between the rotor and stator increases. The air is captured in the different compressor pockets, and decreases in volume with rotation and is later discharged when the vanes pass the outlet port.
Roots Blowers
A Roots blower is a valve-less displacement compressor without internal compression. When the compression chamber comes in contact with the outlet port, compressed air flows back into the housing from the pressure side.
Subsequently, further compression takes place when the volume of the compression chamber further decreases with continued rotation. Accordingly, compression takes place against full counter-pressure, which results in low efficiency and a high noise level. Roots blowers are frequently used as vacuum pumps and for pneumatic conveyance in low pressure applications.